These 8 Problems Are Easily Solved With MRP Software
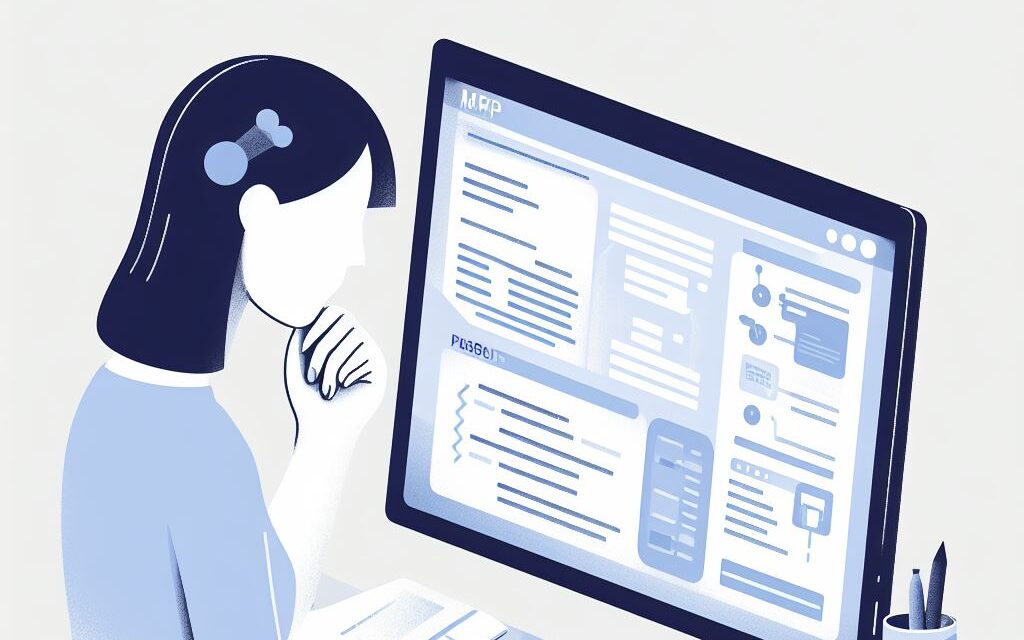
Introduction
The manufacturing sector is no stranger to challenges. From intricate production schedules to balancing inventory levels, the tasks can be daunting, particularly for small manufacturers. This is where MRP (Manufacturing Resource Planning) software like Brytebuild comes into play, transforming challenges into opportunities for efficiency and growth. Let’s explore eight critical manufacturing hurdles and how MRP software provides effective solutions.
The Crucial Role of MRP software in Modern Manufacturing
MRP software is designed to streamline manufacturing processes, bringing a level of precision and control that is pivotal for success in today’s competitive landscape. Let’s explore some real-world manufacturing challenges and how MRP software solutions like Brytebuild effectively address them.
1. Balancing Inventory: Averting Stockouts and Overstocking
One of the pivotal roles of MRP software is to streamline inventory management. Overstocking ties up valuable resources, while stockouts can halt production lines. MRP systems precisely forecast and manage stock levels, ensuring a harmonious balance is maintained. The Chartered Institute of Procurement & Supply offers insights on effective inventory management strategies.
2. Centralising Data Management
Manufacturers often grapple with data management. MRP systems centralise data, allowing for swift retrieval and analysis. This comprehensive data handling improves decision-making and operational efficiency. The UK Government’s guidelines on manufacturing processes underscore the importance of efficient data management.
3. Meeting Regulations
Compliance with traceability regulations is a major challenge in sectors like food and pharmaceutical manufacturing. MRP systems track and document the entire product journey, ensuring compliance and quality control. The Food Standards Agency provides comprehensive guidelines on traceability.
4. Reducing Administrative Burden
Administrative tasks, though essential, can be resource-intensive. MRP software automates these processes, enabling manufacturers to allocate resources more effectively towards production. This UK Business and Industry article discusses productivity enhancement through automation.
5. Handling Complex BOMs
Complex Bills of Materials (BOMs) can be difficult to manage manually. MRP software simplifies this process, supporting intricate product structures with multiple subassemblies, streamlining production planning. The Institute for Manufacturing at the University of Cambridge offers resources on effective BOM management.
6. Facilitating Remote Collaboration
The COVID-19 pandemic has highlighted the need for remote work capabilities. Cloud-based MRP systems like Brytebuild allow seamless collaboration across various locations, maintaining productivity irrespective of physical barriers. Harvard Business Review’s article on remote work trends provides additional insights.
7. Scaling Business Operations
As businesses grow, their operational needs become more complex. MRP software scales with the company, accommodating expanding production requirements without compromising efficiency. The Manufacturers’ Organisation (EEF) offers advice on scaling up manufacturing operations.
8. Streamlining Compliance and Quality Assurance
Ensuring products meet regulatory standards and quality benchmarks is vital. MRP software automates quality checks and compliance processes, safeguarding product integrity. The British Standards Institution provides extensive resources on quality standards in manufacturing.
Brytebuild: Your MRP Software
Brytebuild stands out in the MRP software market, offering a comprehensive suite of features tailored to modern manufacturing needs. From digital work instructions to advanced warehouse management with barcode tracking, Brytebuild ensures that every aspect of your manufacturing process is streamlined and efficient.
Conclusion
Navigating the complexities of modern manufacturing requires tools that are not just robust but also adaptable. MRP software solutions like Brytebuild offer the versatility, efficiency, and precision necessary to meet these challenges head-on, transforming them into opportunities for growth and success.
Explore Brytebuild’s features and register now to revolutionize your manufacturing process!