What are Lot Numbers and How to Use Them in Manufacturing
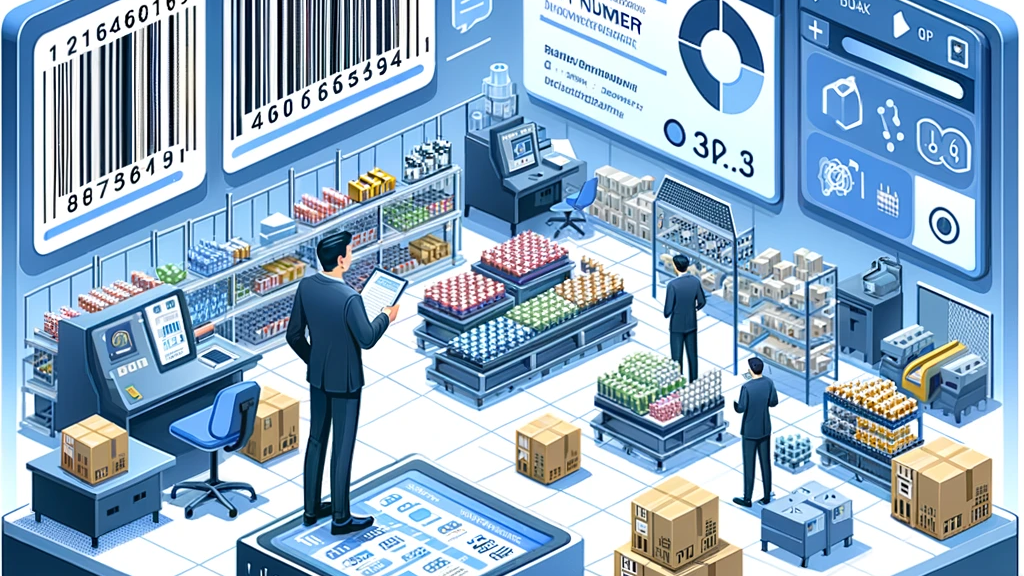
Introduction:
In the world of manufacturing, understanding and effectively managing lot numbers is critical. Lot numbers are not just a regulatory requirement; they’re a cornerstone of quality control, inventory management, and overall operational efficiency. This guide delves into the realm of lot numbers, contrasting them with serial numbers and SKUs, and explores how modern MRP software like Brytebuild can revolutionize their usage.
Understanding Lot Numbers in Manufacturing:
Lot numbers, also referred to as batch numbers, are unique identifiers assigned to batches of products during manufacturing or upon receipt in a warehouse. They play a pivotal role in tracking products through the supply chain, providing essential information like production date, raw materials used, and quality data. For instance, a London-based craft brewery would use lot numbers to track batches of beer, ensuring each meets the high standards expected by consumers.
In-Depth Example: Imagine a pharmaceutical company in London produces a batch of medications on March 15, 2023. The lot number ‘Med15032023’ could be assigned, encapsulating the production date and ensuring traceability.
Lot Numbers vs. Serial Numbers vs. SKUs:
- Lot Numbers: Used for tracking groups of products. Essential in industries requiring stringent quality control, like food and pharmaceuticals.
- Serial Numbers: Individual product identifiers, crucial for items like electronics where warranty and repair histories are needed.
- SKUs (Stock Keeping Units): Help differentiate product variations in inventory systems. Vital for diverse product lines in retail or manufacturing.
Real-Life Application: A London-based electronics manufacturer might assign unique serial numbers to each smartphone for tracking purposes, while using SKUs to differentiate between model variations.
Utilising Lot Numbers for Inventory Efficiency:
Lot numbers can transform inventory tracking, particularly when integrated with Brytebuild’s MRP software. Key steps include:
- Develop a Lot Numbering System: Tailor this to your business needs, incorporating production dates and other relevant information.
- Assign Lot Numbers Efficiently: Utilize MRP software like Brytebuild to automate this process, ensuring consistency and accuracy.
- Comprehensive Record-Keeping: Track production dates, expiration dates, and other critical data within Brytebuild’s system.
- Leverage Barcode Technology: Enhance efficiency and accuracy in tracking lot numbers.
- Efficient Inventory Tracking: Use Brytebuild to monitor inventory levels and movement, ensuring you’re always on top of stock management.
- Facilitate Quality Control and Recalls: Quickly isolate and address quality issues or recalls by tracking affected product batches.
Implementing Lot Numbers: A Step-by-Step Guide
- Designing a Lot Numbering System: Kickstart your journey by crafting a bespoke lot numbering system that suits your business needs. A lot number might look like “Batch20230705”, symbolizing a specific production date. This system should be straightforward yet comprehensive, encompassing crucial details like manufacturing dates and batch sizes.
- Lot Number Assignment: As products roll off the production line or arrive in your inventory, assign them their unique lot number. This could be through automated systems or manually affixed labels – the goal is to ensure every batch is clearly marked and distinguishable.
- Detailed Record-Keeping: With each lot number, document vital information such as raw material sources, production processes, and quality checks. This data becomes invaluable in times of need, such as product recalls or quality audits.
- Embracing Technology: Implement barcode scanning for efficient tracking and management. This modern approach not only saves time but also significantly reduces human error in inventory management.
- Lot Number Utilization: Use lot numbers to monitor stock levels, track product movements, and manage expiration dates. This is especially crucial in industries with perishable goods or products with a limited shelf life.
- Quality Assurance: Regularly conduct quality checks based on lot numbers. This ensures that any potential issues are isolated to specific batches, preventing widespread problems and maintaining product integrity.
- Software Solutions: Consider investing in a Manufacturing Resource Planning (MRP) system that supports lot number tracking. Such systems can automate many of the processes involved in lot number management, from inventory tracking to quality control.
Choosing the Right MRP Software for Lot Number Management
When selecting an MRP system, look for features that cater specifically to lot number management. The ideal software should offer seamless integration with your existing processes, providing a bird’s-eye view of your inventory and enabling you to trace each product’s journey from raw material to finished good.
The Role of MRP Software in Lot Number Management: Brytebuild’s MRP system simplifies lot number management, offering benefits like:
- Seamless Integration: Incorporates lot number tracking into overall inventory management.
- Enhanced Traceability: Essential for industries with strict regulatory requirements.
- Streamlined Operations: Automates lot number assignments, reducing manual errors.
- Effective Quality Control: Facilitates batch-specific quality checks and compliance.
Practical Example: A small London-based food producer could use Brytebuild to manage lot numbers, ensuring compliance with UK food safety standards and enabling quick responses to potential product recalls.
Key Takeaways:
- Essential for Quality and Compliance: Lot numbers are crucial in ensuring product safety and meeting regulatory standards, particularly in sectors like pharmaceuticals and food production.
- Varied Yet Complementary: Lot numbers, serial numbers, and SKUs each serve unique and vital roles in inventory management.
- Enhanced by Technology: Modern MRP software, like Brytebuild, offers an efficient, error-reducing approach to managing lot numbers.
Frequently Asked Questions:
- Q: How do I create a lot number? A: A lot number can be created by combining relevant information like production date and batch size into a unique code. Consider using a format that’s easily decipherable and consistent across your product range.
- Q: Why are lot numbers crucial in manufacturing? A: Lot numbers are essential for traceability, quality assurance, regulatory compliance, and efficient inventory management. They enable manufacturers to track the journey of each product, ensuring safety and reliability.
- Q: Where should lot numbers be placed on products? A: Lot numbers should be prominently displayed on product packaging or labels, ensuring they are easily accessible and readable for both inventory management and consumer information purposes.
Discover how Brytebuild can elevate your lot number management and overall inventory efficiency. Explore Brytebuild features and witness the transformation in your manufacturing processes today.